Materials
ou understand how RF absorber works, appreciate why its pyramidal shape influences performance, can describe how it’s specified for performance, know how to select the correct length and shape for your application, and understand how it is manufactured and how the manufacturing process affects absorber quality. These are all great attributes of RF absorber that you must take into consideration when properly outfitting an anechoic chamber for EMC testing purposes. But have you also considered safety attributes, including the maximum power handling capability the absorber will need to meet in your application and also its flammability rating? The safety performance specifications of RF absorbers are just as important as the other attributes of RF absorber performance. Let’s talk about them next.
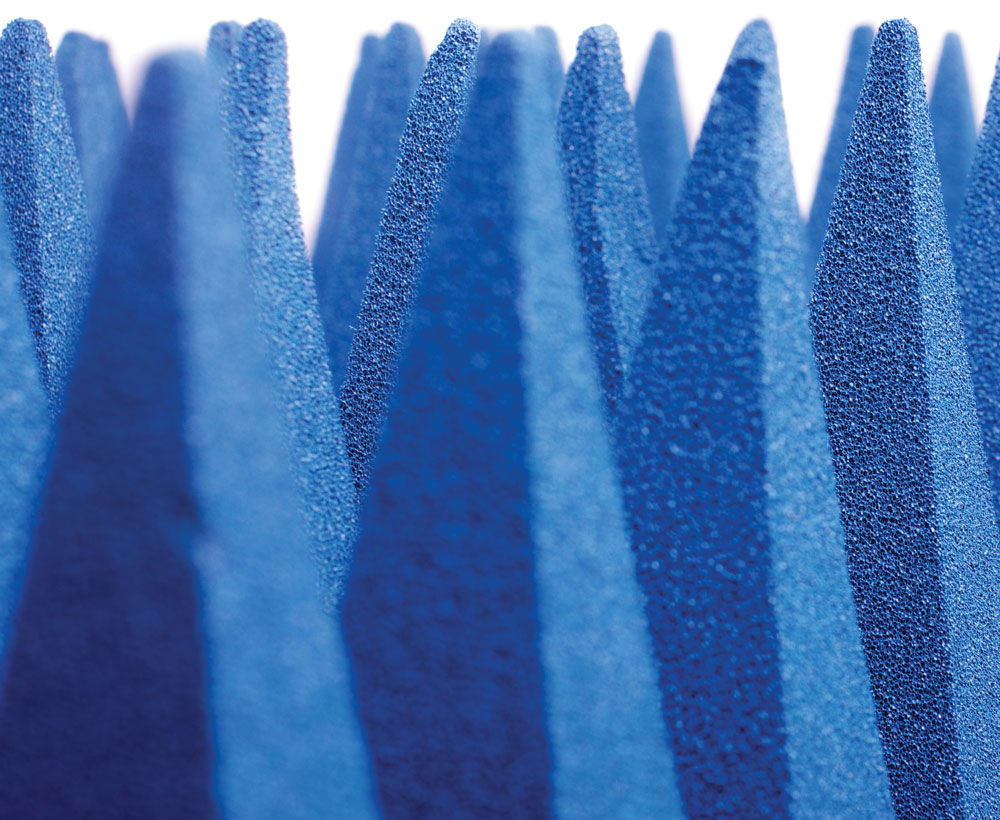
- DIN 4102 Class B-2
- MIT Lincoln Laboratory Specification MS-8-21 (Tests I, II, and III)
- NRL Report 8093 (Tests 1, 2, and 3)
- Raytheon Drawing No. 2693066 (latest revision)
- UL 94 HBF
- UL 94-5VA and UL 94-5VB
WARNING: The above information is only a guideline into a very complicated subject on absorber RF power handling capability. As with most things in EMC, there are a lot of variables to consider. These variables include frequency range of testing, near or far-field conditions, ambient temperatures, and air flows (or lack thereof). Before selecting any particular RF absorber solution, it would be wise to conduct an extensive power handling study using simulation tools that produce results that are backed up by real-life test data. Consult the reference for more information.
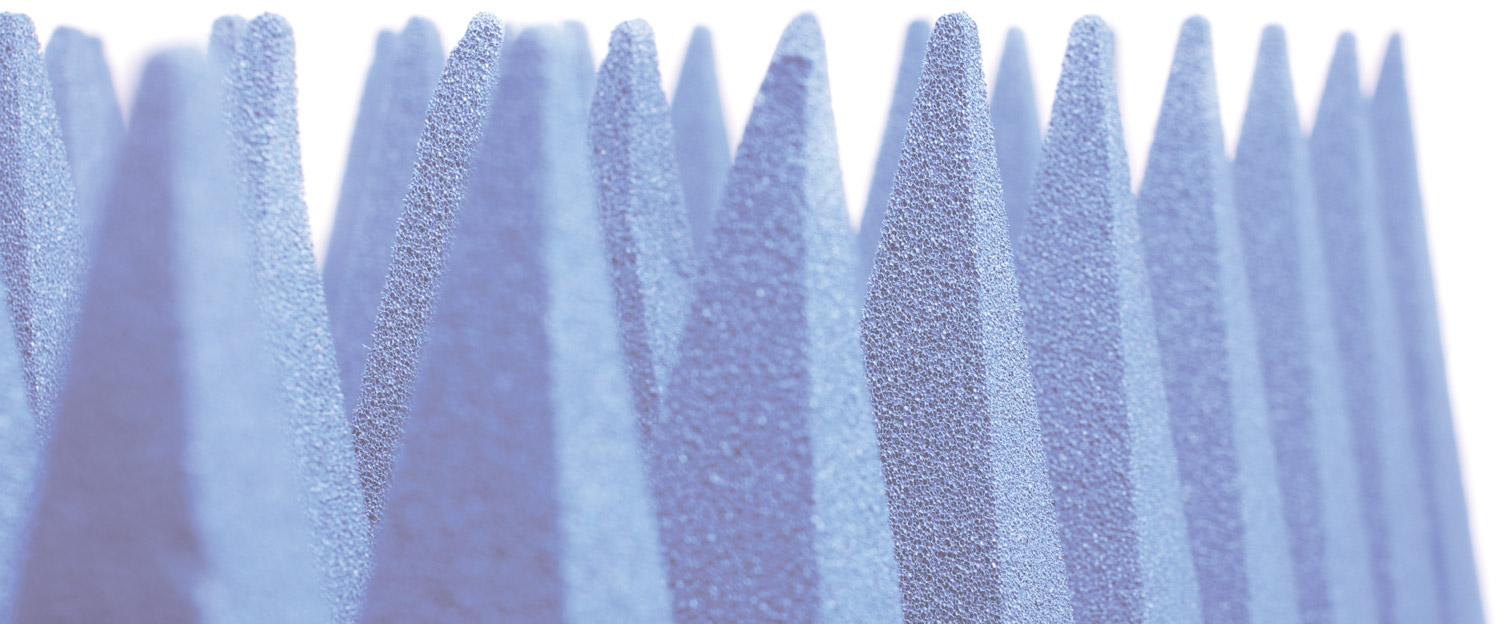
- Know how anechoic absorber works. Absorber is designed to reduce reflections from impinging electromagnetic (EM) waves, and “absorb” incident EM energy.
- Match absorber design to application. Absorber works by dissipating the EM energy inside the absorber and turning it into heat. In most RF, microwave and antenna applications, the lossy dielectric works best because of superior EM absorption at higher frequencies.
- Pyramidal shape influences absorber performance. Broadband absorbers work by avoiding “sudden” changes in impedance for the impinging wave and gradually terminate and absorb the EM wave.
- Specify absorber for RF performance. Absorber is specified for reflectivity as a function of frequency at normal incident angle. Understand that reflectivity degrades at larger incident angles
- Match absorber length and shape for your application. Pyramidal absorber length determines how well it can work at the lowest frequencies.
- Use commonly available absorber lengths. Save money, speed delivery by choosing absorber in typical, off the shelf lengths.
- Determine maximum power handling capability of absorber. Polyurethane absorbers are specified to withstand a maximum power of W/in2 of continuous wave (CW) incident field under room temperature with no additional forced airflow.
- Manufacturing process impacts absorber quality. Find a computer controlled manufacturing process that begins with homogeneous blocks of polyurethane foam.
- Use non-hygroscopic absorber. Maintain a stable absorber electrical property and RF reflectivity by reducing moisture, which affects electrical conductivity significantly.
- Confirm RF performance verification testing. Ask how your supplier tests the absorber to verify performance reflectivity before shipment. Is each piece of absorber tested or sample tested one piece per batch? Is each piece serialized? Ask these questions protect your investment!